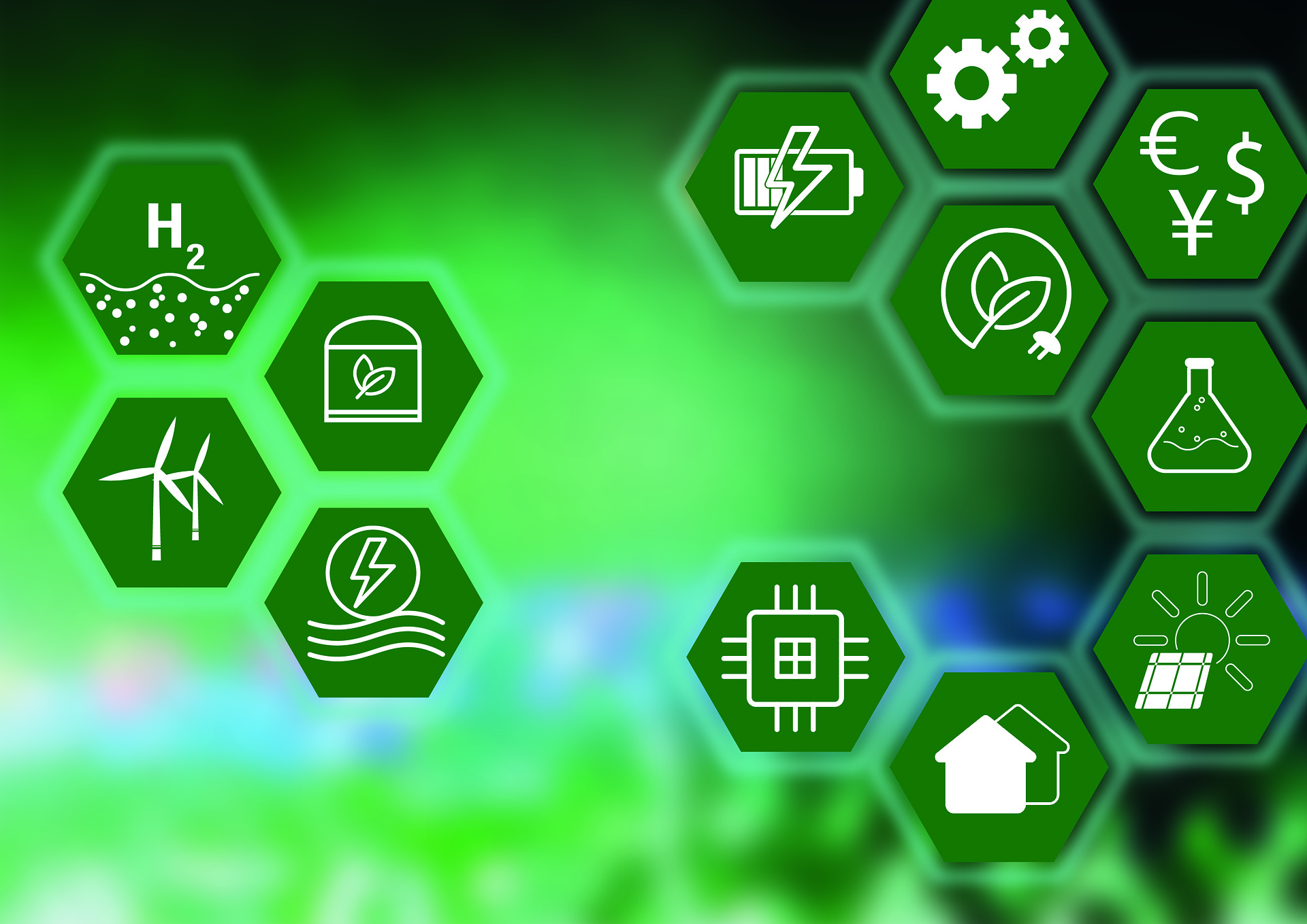
The discovery that existing Oliver Valves technology had been successfully deployed by key customers into the Hydrogen and Carbon Capture markets sparked the interest of Chairman Michael Oliver. Seeking to develop this potentially lucrative market further, Oliver Hydcovalves Ltd was incorporated as the vehicle for this exciting diversification.
The UK is setting the pace as a world leader in developing a zero-carbon economy. In order to achieve this ambitious objective, many of our traditional hydrocarbon reliant industries will need to transition to green energy sources such as Hydrogen or clean up their CO2 greenhouse gas emissions through the use of Carbon Capture and Storage (CCS) technologies.
The rest of the world is following closely, driven by the 2015 Paris Agreement, which set a limit on global warming to below 1.5 degrees Celsius by the mid-century.
Oliver Hydcovalves, a ‘‘green’ company has been set-up to pursue our interests in supplying valves into the hydrogen and carbon capture markets.
Nick Howard, Tony Goodwin and Rob Porter are taking the responsibility to move this new Company forward with new product designs to meet the requirements for hydrogen and carbon capture applications. This is part of worldwide efforts on climate change and, most significantly, achieve zero emissions by 2050.
Continual improvement through the Oliver Research & Development team will ensure our valves continue to meet or exceed the technical challenges presented by these emerging applications; for example, new materials which prevent the action of Hydrogen Embrittlement.