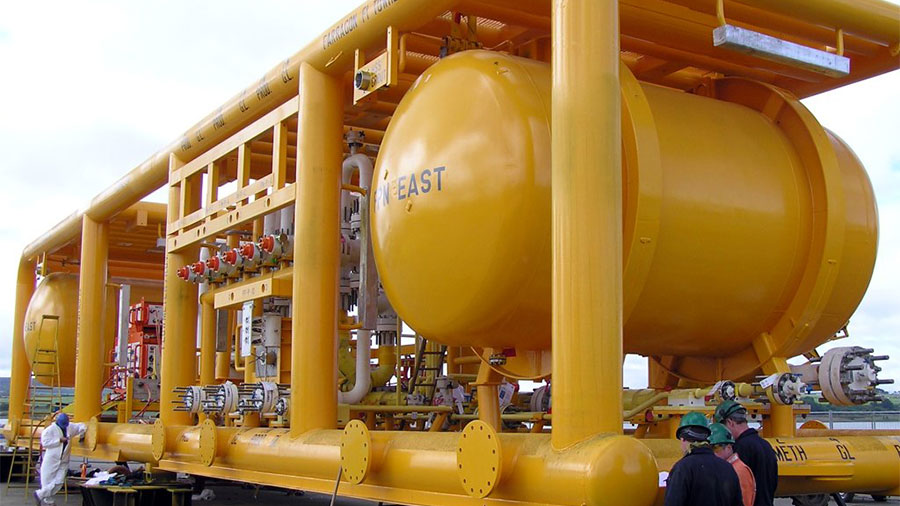
Several issues need to be considered to design and configure a subsea development controlled and operated over a significant distance.
Various industries use subsea valves, with the oil and gas sector accounting for the majority, as there is a need to move material from, to, or below the seabed. Subsea valves are used in sub-marine environments, ranging in depth from shallow water (usually down to a depth of 75 meters) to Ultra-deep water (down to 3000 meters).
In today’s offshore oil and gas industry, wells have become deeper than ever, causing a growing demand for subsea ball valves that can withstand extreme pressures and harshest environments.
At Oliver Valvetek, we are a leader in developing ways to provide effective valve solutions under increasing temperature and pressure requirements at greater depths, offering subsea Needle, ball, Gate and Check valves that provide safe and reliable operation at very high external pressures.
What Are SubSea Valves?
Subsea valves are used to isolate or control the flow of material through an undersea Christmas tree, Subsea manifold, SDU, UTA or pipeline (submarine pipeline) or other subsea architecture. They are most commonly used to transport oil and gas or for chemical injection applications to ensure the continuous operation of the subsea installation. They are designed to function in a submarine environment while withstanding the effects of raised external pressure, wellbore temperatures, environmental conditions or debris in the material passing through the valve.
At Oliver Valvetek, our Subsea valves undergo stringent testing to ensure high Safety, Quality and reliability, assuring their Quality Assurance and Quality Control before being used in the industry. External environmental factors need to be explicitly considered for subsea valves. This includes specialist anti marine coating systems, High operating temperatures and pressure, and ensuring the valves are protected by the subsea systems Cathodic Protection (CP).
Subsea control systems
There are two different types of subsea control systems. Firstly, a basic control system, which is used to control normal operations of the subsea production system. Secondly, a safety control system is used to control abnormal incidents and avoid accidents by isolating the energy source.
Our knowledge in the oil and gas industry is combined with highly experienced engineering and modern production facilities allowing us to fulfil almost all requirements for subsea installations. Subsea valves are generally exposed to extremely harsh conditions, whether this is extremely high pressures, low and high temperatures, chemical interactions, or a combination of these. Attention to detail is required and recommended; as a trusted supplier over 125,000 subsea valves, we understand where valves are used as a necessity.
While some valves may be manually operated by divers, the majority are either manually operated by a Remote Operating Vehicle (ROV) or hydraulically operated subsea valves controlled via topside. If this is the case, unique connections are required to ensure that the paddle or drive adapter is compatible with the valve as well as the ROV.
Hazards to Subsea Valves
Internal factors to consider for subsea valves are related to the type of process media (what passes through the valve apparatus). Typically in subsea environments, the process media will either be liquid, gas-based or a mixture of both. Additionally some processes due to the location of the operation, the process can also contain a significant amount of sand and debris. This can present several adverse effects including:
- Erosion of the valve internals
- Damage to stem and seat sealing faces within the valve
- Blocking of valve process flow paths within the valve
For more information about our Subsea valves, why not get in touch with Oliver Valvetek today?